Table of Contents
We’ve seen many companies who have tried improvement after improvement year after year. Many of these have been applied in parallel e.g. CMMI and ISO9001, CMMI and 6 Sigma, Lean and EFQM and GQM. Others apply them in a more serial manner: ISO9001, GQM, CMMI, 6 Sigma, Lean, Agile, TDD, Continuous Delivery.
Yet after a time most of these initiatives splutter and fade into obscurity.
Often the reasons are obvious:
-
was the flavor of the month
-
an executive had a bee in his bonnet
-
the organization’s objectives weren’t aligned
-
a company’s business model had changed
-
staff felt it had become a ‘going through the motions’ exercise
-
and a whole heap more you could add yourself
But often the methods are implemented with the best intentions.
How can they go wrong?
A multifaceted approach can often work best since most organizations are not homogenous and have different strengths and weaknesses – just like the improvement models themselves – they each have areas that they excel in and organizations for which they are not appropriate (e.g. CMMI in a 2 person company).
Whilst many have tried (and are still trying), there is not yet a Grand Unified Theory of business and process improvement.
But in adopting a multi-model approach an organization needs to be careful to select the most appropriate situation for each model they want to engage.
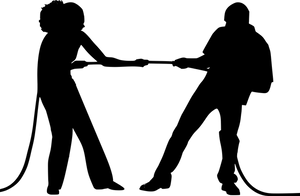
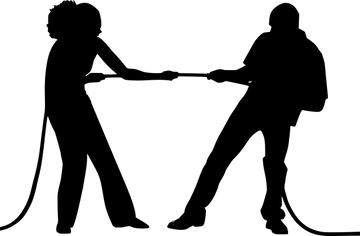
It is difficult to visualize all of the improvements from all of the initiatives and how they are engaging the other initiatives – instead, each initiative develops a bubble around it – taking more projects and activities into scope.
Similar to physical bubbles each initiative grows or shrinks depending on the pressure from inside supporting it and the pressures from outside restricting it in size.
Occasionally two bubbles will touch and unless this event is handled explicitly, one or more bubbles may burst.
A better solution is to ensure each initiative clearly defines what it will do with the processes, areas/projects/tasks, cultural behaviors that it has in common (where it “touches”) with the other initiatives.
As noted above, many methods appear to extol the same virtues and build up a strawman of other methods to differentiate themselves. The implementation is often lacking in specifics to show differences to those who have come before.
While some SPI approaches provide guidance for selecting them e.g. good for safety-critical domain, bad for teams > 50 people – generally these tend to blend and an ad-hoc approach is taken (often by default). This means that many companies have a multitude of improvement approaches – some new, some legacy and other just vague remnants of what happened before.
We’ve all seen TQM, Quality Circles, Deming and other approaches lurking about the place – some still used, others still around but no one knows why and what it was supposed to be for.
Typically when an organisation has staff turnover, they lose a lot of corporate memory. Sometimes the turnover includes PI sponsors, champions or similar. The remaining staff then have to pick up the pieces and carry on – but because of the budget cuts that invariably accompany these turnover re-orgs, carrying on is rendered almost impossible except to use a template here and a form there.
What is lacking?
A whole of business i.e. portfolio view of improvement initiatives. Ask yourself:
-
have we identified all of our current (and remnant) improvement and change initiatives
-
are these initiatives still happening?
-
have they been institutionalised/operationalised?
-
how committed are staff to them?
-
how do they align with current company objectives, structure, focus, direction, technologies?
-
can they be prioritised?
It’s this prioritisation process that enables a purging of unused activities and initiatives. If a method or improvement approach is still about but hasn’t been used or touched in 6 months, you can be pretty sure it can be dropped. Do a lessons-learnt or retrospective, use what you can and close down the initiative. By doing this the improvement initiatives can remain fresh, relevant and focused on what is needed.
Whilst cost-benefit calculations are notoriously difficult due to competing projects and compound variables e.g. was the defect rate reduction due to the ISO9001 initiative or a peer review process as instigated by CMMI? Or was it a technology improvement?
Even still, by looking at the tasks implemented including:
-
what was intended
-
cause/effect
-
what occurred
We can begin to identified potential weightings of attributes from each SPI approach and then use this as a basis of comparing impacts from improvement methods and their eventual impact on company objectives.
James Kelly is CEO of Method Buzz, a boutique consultancy providing strategic ICT advice, software & system engineering method transformations in defence, aerospace, telecommunications, and software start-ups. After graduating with a Bachelor of Informatics and an MPhil from Griffith University, he helps clients in the practical application of high maturity methods in quality and organisational improvement. Partnering with client teams, Method Buzz brings about significant productivity and quality improvements in organisations within engineering and technology. James has had a lifelong fascination with Wicked Problems and how to manage them.
This article does not constitute legal advice.
The opinions expressed in the column above represent the author’s own.
Start managing your legal needs with Zegal today
BECOME A ZEGAL REFERRAL PARTNER
READ MORE:Social Media Marketing Tweaks That Could Change Your Business
Article syndicated with permission from https://www.methodbuzz.com/post/a-bubblepoint-view-of-agile-cmmi-and-other-quality-improvements
MethodBuzz helps you and your organization to identify, understand, prioritize and solve your critical business problems. With so many methods, processes, techniques being introduced continually, it can seem daunting to stay on top of things and determine which are useful to your organization, people, processes and problems.
They use the OODA (Observe, Orient, Determine, Act) loop to accelerate your decision making and operations business processes. By taking a business problem-oriented approach to analyse and plan improvements you can stay focused on the things that matter.